[ad_1]
Cotton is likely one of the most precious crops grown within the U.S., with a harvest worth of some US$7 billion yearly. It’s cultivated throughout a crescent of 17 states stretching from Virginia to California and is utilized in virtually every type of clothing, in addition to in medical provides and residential items comparable to upholstery.
Cotton grows inside a tough, fibrous case referred to as a boll. About 100 days after planting, the bolls mature and break up open, revealing 1000’s of fluffy white fibers inside. Every boll accommodates 20 to 40 seeds with fibers connected to them, which is why the cotton plant’s fruit is known as seed cotton.
Choosing cotton manually, as remains to be completed in some major producing countries, is a meticulous process. Employees must bend to achieve the bolls and may damage their fingers on hard, dry parts of the plants. To reap the seed cotton, they must seize and twist it to separate it from the boll with out leaving fiber behind.
Beginning within the Nineteen Thirties, cotton farmers within the U.S. shifted from handbook labor to large, heavy harvesters. Now the trade is getting into a brand new stage that guarantees to be extra environment friendly and exact.
I’m an engineer and have nearly 20 years of research experience engaged on agricultural equipment. My present focus is on agricultural robotics and automation. Throughout my Ph.D. program at Mississippi State College, I labored with Alex Thomasson, who heads the agricultural and biological engineering department and the Agricultural Autonomy Institute, to develop a robotic cotton harvester that picks cotton with much less harm to the product and the soil the place it grows.
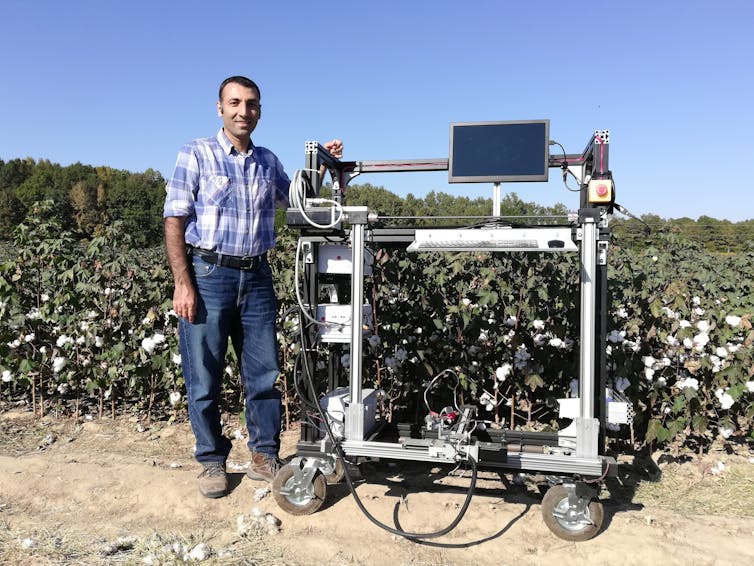
Hussein Gharakhani, CC BY-ND
Why use robotics?
Cotton farmers have financial, environmental and agricultural causes to need a greater possibility for harvesting. Conventional mechanical harvesters might be as much as 14 ft lengthy and weigh greater than 30 tons. They take away cotton successfully with out damaging the vegetation but in addition may cause issues.
One situation is extended fiber publicity. Cotton bolls don’t all mature on the similar time; the primary open bolls in a discipline might watch for as much as 50 days to be picked, till extra bolls round them ripen.
One other problem is that harvesting machines compact the soil as they roll over it. This makes it more durable for water and fertilizer to penetrate all the way down to plant roots. And the machines price roughly US$1 million apiece however are used for less than two to 3 months every year.
Robotics is a possible resolution that farmers are already utilizing for different crops, comparable to fruits and vegetables. Harvesting robots use cameras and sensors to detect when crops are prepared to choose and may take away them with out damaging the plant.
For cotton, robotics gives extra focused choosing of bolls which can be prepared to reap. It produces better-quality cotton fiber by choosing seed cotton as quickly because the bolls open, with out leaving it uncovered to the climate. The robotic targets the seed cotton and avoids touching different components of the plant.
With robotic choosing, cotton farmers don’t need to use defoliants to take away leaves from the vegetation previous to harvesting, which is a standard follow now. And small, nimble robots don’t compress the soil as they transfer over it, so they assist preserve soil well being.
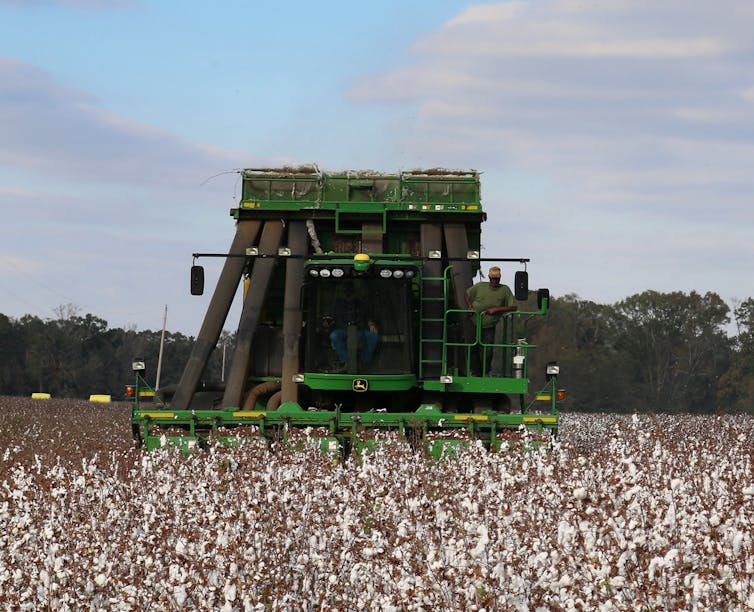
Katie Nichols/Alabama Extension/Flickr
A bioinspired ‘choosing hand’
Our work focuses on designing an end-effector for robotic cotton harvesting. An end-effector is a robotic hand that allows the robotic to work together with different objects. Ours is a three-fingered model designed for delicate and environment friendly cotton choosing. It attracts inspiration from nature, mimicking the searching prowess of a lizard.
Every finger is a 3D-printed construction that accommodates a shifting belt with pins connected to it. The pins assist the hand grasp and pull within the seed cotton. Like a lizard snatching prey with its sticky tongue, our end-effector’s three fingers method the seed cotton delicately. On contact, the cotton fibers keep on with the machine’s fingers, a lot as an insect sticks to a lizard’s tongue.
Subsequent, the hand retracts shortly, just like the lizard’s tongue. The top-effector retains working to “swallow” the seed cotton, transferring it out of the plant. Because the harvester picks and transfers seed cotton out of the plant, the end-effector touches components of the cotton boll with remaining seed cotton a number of occasions to choose as a lot as attainable.
To select cotton effectively, our robotic has to do three issues: detect bolls which can be prepared for harvest, decide precisely the place they’re positioned in a three-dimensional area and choose the cotton.
The robotic makes use of a deep-learning algorithm that we have now educated to acknowledge open bolls on cotton vegetation. It makes use of a stereovision digital camera to calculate their 3D spatial coordinates, which it transfers to the robotic arm. A management algorithm screens every cotton boll to make sure that the robotic picks as a lot seed cotton as attainable.
Testing and outcomes
Thus far, we have now examined the robotic cotton harvester in the laboratory and in cotton fields. The detection system discovered 78% of ripe cotton bolls; the localization system calculated 3D coordinates for 70% of the detected bolls; and the choosing system efficiently harvested 83% of those bolls. General, the robotic picked about 50% of the cotton bolls that have been inside its attain.
Our harvester picked cotton at a pace of 8.8 seconds per boll. If we will lower this required time to 0.3 seconds and enhance the robotic’s effectivity to choose at the very least 90% of the cotton bolls it might attain, by optimizing the system and including extra arms on a robotic, a fleet of fifty robots may harvest a cotton discipline as shortly as a mechanical harvester, with a comparable yield.
To enhance the robotic’s total efficiency, we plan to undertake higher synthetic intelligence algorithms, enhance our system’s digital camera and add one other diploma of motion to the robotic arm – for instance, enabling the end-effector to rotate – to extend its dexterity.
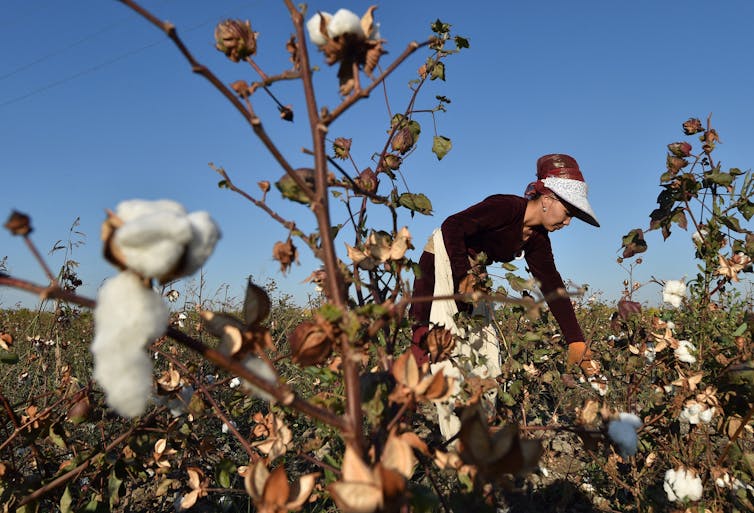
Vyacheslav Oseledko/AFP via Getty Images
We see nice potential for our robotic in main cotton-producing international locations comparable to China, India, Pakistan and Uzbekistan, the place cotton is at the moment picked by hand, typically by women and children and typically under abusive conditions. One strategy to make this expertise accessible for small farmers in low-income international locations could be to make smaller, semi-autonomous robots that might require fewer sensors. Producing higher-value cotton with much less harm to vegetation and soil may enhance life for hundreds of thousands of people that earn their livings elevating this international crop.
[ad_2]
Source link